Published on the 07/05/2024 | Written by Abel Software
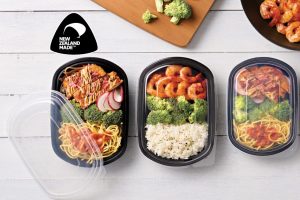
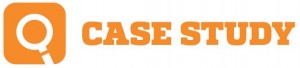
AT A GLANCE
INDUSTRY
Food packaging producer
BUSINESS OBJECTIVES
- Affordable, integrated ERP tools to deliver full visibility and accuracy of financials, inventory management and production.
- Consolidated views of financial performance across three companies to optimise business efficiency, reporting and profitability.
- Material Requirements Planning (MRP) functionality and seamless integration with Bonson’s existing AspectPL manufacturing execution software, developed by Abel associate, Aspect Productivity Technology.
SOLUTION
- Single, seamless ERP functionality to integrate separate systems, including financials, manufacturing and inventory management.
- Automated workflows to replace manual processes, including the use of handheld devices to update and integrate inventory data directly from the warehouse floor.
- Smooth implementation, including integration of existing Aspect MES, to avoid costly downtime and business interruptions.
- Flexibility to roll out additional ERP functionality as required.
BUSINESS BENEFITS
- Streamlined business processes with greater overall efficiency.
- Real-time visibility and traceability of manufacturing and production processes, stock and material requirements, and group financials.
- IConsolidated financials and reporting tools with the visibility to accurately measure performance and make the right business decisions at any time.
CONTACT DETAILS
Abel Software
W: www.abelsoftware.com
New Zealand
T: +64 9 526 5210
Melbourne, Australia
T: +61 2 9888 3355
Sydney, Australia
T: +61 2 9888 3355
Bonson NZ packages up ERP success with Abel…
A leading Australasian producer of food packaging, Bonson NZ chose Abel® to integrate their manufacturing systems and automate production workflows – delivering greater visibility and accuracy of critical data and improving overall efficiency.
Bonson NZ knows that good things come in small packages.
“Before Abel I believed there were only two types of ERP implementations – bad and really bad.”
For the past 40 years, the award-winning company has designed and manufactured innovative and customised packaging to keep products fresh and safe for all kinds of food makers and suppliers – from cafes, caterers and takeaways to ice cream makers, restaurants and supermarkets.
Growing from a small family-owned business to a leading international brand, Bonson now produces thousands of packaging solutions across eight brands of recyclable, bio-degradable and compostable products. These range from bespoke tamper-evident packaging to the popular clear rectangular takeaway container, of which Bonson produces tens of millions a year.
After opening a purpose-built Auckland manufacturing facility to accommodate export growth, larger production runs and tighter order deadlines, Bonson began to search for an ERP system to drive greater efficiency and visibility of critical financial and operational data.
“We had a great manufacturing management system with AspectPL and some basic accounting packages but not much else,” says Rodney Bennett, who joined Bonson in 2020 as the Business Development Manager.
“We had no accurate visibility of our business, no demand planning or cost analysis, and no inventory management system. Previously, if we wanted to know if we had stock on hand to fill a new job, someone would literally walk around the warehouse aisles until they found it on a pallet.”
Bonson’s need for an ERP system was clear, but Rodney took a careful and cautious approach to choosing a provider, owing to his experience installing an ERP system with another food packaging manufacturer.
“My previous experience was a nightmare. We had to take six people out of the business for six months to help design the system. And when the system went live, it still went belly up. We couldn’t even deliver stock to customers. It took months to sort out even the basic problems, and years before the system ran smoothly.”
“Before Abel,” he says, “I believed there were only two types of ERP implementations – bad and really bad.”
Bonson considered an initial field of 25 providers before choosing Abel.
“We had a good feeling about Abel from the start,” Rodney says. “We saw what they had done for other companies, they offered local support, and they were always positive, collaborating on the integration of our Aspect MES tool and assuring us our implementation would take only three months.”
Abel went live in October 2022 and, Rodney says, it has been running smoothly ever since.
“I had two basic metrics we wanted to meet immediately – delivering products to our customers and sending out invoices – and Abel did it easily. We had lots of people supporting us and it was a very good and easy transition.”
One significant benefit Abel delivers to Bonson is the consolidation and integration of financial information across three companies: Bonson NZ, Bonson Australia and SavPac, an importer of environmentally friendly food service tableware and packaging.
“This doesn’t just give us greater accuracy and visibility of our financials at a group level,” Rodney says. “It also delivers easier and better reporting and will help us make more informed business decisions now and in the future.”
Abel also optimised Bonson’s inventory management by providing real-time visibility of stock flows, making it easier to fulfil orders on time and in full. For example, workers in New Zealand and Australia now use handheld devices on the warehouse floor to accurately record and transfer stock, complete orders and confirm shipping details in Abel.
“We were wasting a lot of time before trying to find stock when an order came in, but not anymore,” Rodney says. “The beauty of Abel is that everything is linked together and we have so much more visibility of stock and raw materials.
It’s not hard to sing Abel’s praises. It’s a fantastic system that makes things a lot easier for our whole business. I would recommend it to anyone.”
Rodney says Bonson is just scratching the surface of Abel. They hope to utilise more of Abel’s Material Requirements Planning functionality to enhance inventory control, demand planning and purchasing.
“We’re starting to use more and more of the system,” he says. “We’re not yet using Abel to cost our products but it’s something we’re looking to do soon. It’s the only easy and accurate way for us to understand our true costs and profitability.
“That will be yet another powerful tool in Abel to drive our efficiency.”
FURTHER READING
About This Vendor
More Case Studies

New ERP provides help with the heavy lifting
Victor Hydraulics leverages Abel ERP for system replacement…

Cakes and donuts get a sweet ride with new ERP
Mitigating recall risk just one factor in new system for Original Foods Baking Co.…

Traceability adds unique factor for NZHF honey
Manuka honey exporter NZ Health Food Company has embraced ‘all-in-one’ ERP solution Abel…

A honey of a solution for Taupo exporter
Cosana is enjoying sweet success with Abel ERP’s traceability, flexibility and ease of use…

Rising to the top with real-time data
When divestment prompted leading NZ dairy solutions provider DTS to transform their systems, they turned to Abel ERP…