Published on the 11/09/2008 | Written by Infor
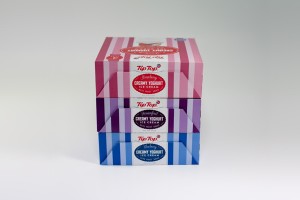
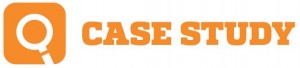
AT A GLANCE
INDUSTRY
- Food Manufacturer
BUSINESS OBJECTIVE
- Business growth was placing a heavy demand on Tip Top’s manufacturing processes so the company sought ways to minimise production downtime and deliver production efficiencies at the same time as ensuring that quality standards were maintained.
SOLUTION
- Infor SCM Demand Planning
- Infor SCM Advanced Scheduling and Infor SCM
- Rough Cut Capacity Planning, all implemented by EMDA.
THE BENEFITS
- Improved scheduling is saving Tip Top an average of $17,000 a month in reduced wasted raw materials and has resulted in a 35% reduction in plan changes.
FOR MORE INFORMATION
INFOR
W: INFOR
T: +61 2 9021 7100
PARTNER CONTACT
EMDA
W: EMDA
T: +64 9 921 6600 or
T: +64 3 343 0023
E: info@emda.co.nz
Smart demand planning and scheduling solutions have helped the iconic ice cream maker optimise production and lick the expensive issue of raw material wastage…
Generations of New Zealanders have a soft spot for Tip Top. Since 1936 its ice creams have been as much a part of the summer ritual as cricket, Christmas and daylight saving.
Producing approximately 50 million litres of ice cream each year, the company’s influence has spread overseas with exports to Australia, Singapore, Malaysia, Taiwan and the Pacific Islands.
Operating in a market subject to seasonality and the fickle whims of food fashion, Tip Top’s longevity can be attributed to a culture of innovation in food manufacturing. Part of dairy giant Fonterra, Tip Top employs approximately 400 staff and distributes its products through grocery channels, dairies and other retail food outlets.
Capacity and demand planning
Ice cream manufacturing is a thriving industry and Tip Top is reaping the benefits of strong local and international demand.
The company is growing, as is the volume of ice cream it produces each year. It’s a situation designed to make any shareholder happy but one that also requires strong management to maintain control over both quality of product and production.
One of the measures that has helped Tip Top in recent years has been its willingness to complement the company’s ERP system with supply chain management (SCM) applications.
Tip Top took its first steps in this direction a little over three years ago when it purchased Infor SCM Rough Cut Capacity Planning.
The software enables Tip Top to confirm capacity by comparing known demand against production commitments. It indicates where resources may need to be increased and helps with decisions such as pre-building of stock.
Two years later, when moving its Christchurch manufacturing activities to Auckland, the company saw an opportunity to extend its use of SCM to bring greater control to production and scheduling.
“Ice cream manufacturing involves a maturation process whereby you take the raw ingredients, put them into a tank, mix it all, pasteurise it and freeze it before putting it into a tub,” explains Andrew Goodin, supply planning and procurement manager at Tip Top.
“It sounds simple but the process demands precise timing and rigorous attention to detail. The mix can only remain in the tanks for a certain period of time before the product must be used or dumped. Any mistakes or delays can result in thousands of dollars of wasted raw materials,” he says.
“We wanted help to operate production and scheduling in the most efficient way possible and at least cost. Our current ERP platform was fairly old and extending functionality wasn’t an option, so we began looking at supply chain solutions. We wanted not just an integrated option but a best-of-breed solution to the problem.”
In early 2007 Goodin approached Infor and its local partner, EMDA. In February the three companies began working together to deploy Infor SCM Demand Planning. The software enables Tip Top to determine demand for ice cream sales over the coming 12 and 18 months, breaking the data down to the level of each individual SKU.
“It takes our demand history and adds in promotional plans, market intelligence and new products and provides us with unconstrained demand data,” Goodin says.
The importance of scheduling
Just a few months later with Demand Planning bedded in, Tip Top extended the implementation by deploying Infor SCM Advanced Scheduler, a tool that offers finite capacity scheduling for batch-process production facilities.
The software optimises productivity by minimising changeover times and improving delivery performance. Critical to Tip Top’s decision was the software’s tank optimisation and scheduling for liquids.
“Infor and EMDA had provided good service in the past,” Goodin notes.
“Infor came out and did a pilot in just three days which was impressive and certainly got the executive team on-side. The model that they developed has ended up being the one that we now use with only a few additional customisations.
“The application models any manufacturing constraints,” Goodin continues. “For Tip Top that may be things like ingredient feeders or the sequencing of products.
For example if we want to make three different ice creams we need to schedule them in sequence to minimise the number of cleans required, so we would go from vanilla to strawberry to chocolate,” he says.
“Getting it in the right order reduces machine downtime. The software also helps us to arrange schedules so that we minimise the number of times we need to change moulds and finds ways to use the least amount of resources.”
Avoiding the cost of change
Goodin’s faith in the best-of-breed approach has paid off with up to 35 percent reductions in plan changes as a result of better sequencing.
“There’s also been a slight drop in resource cost,” he says.
“We’ve improved the way our tank farm operates and this has helped us to minimise waste. Over the last month it saved us about $17,000 in materials that would otherwise have had to be dumped. It would be a similar amount that we are saving each month.”
Tip Top’s return on investment for the SCM project called for more efficient planning and greater adherence to the production plan. Goodin is confident that this has been achieved. “We’ve reduced overall costs by sticking to the plan. We are avoiding the costs of change,” he says.
Lessons learned
When asked what advice he has for other organisations considering going down the SCM road, Goodin suggests: “Go with a specialty supply chain product that integrates well with your ERP platform. The Infor and EMDA team were excellent and provided real value. Secondly, make sure you understand your business and your business processes. You’ll get better value out of it if you do. Finally, make sure that all along the way you train and up-skill your own people so that you can take over the serviceability of the environment.”
“Our supply chain strategy is ‘Simplicity’ – the Infor tools have reduced complexity and allowed us to simplify our planning and improve visibility – ultimately delivering more to the bottom line” he says.
Goodin is keen to continue to develop Tip Top’s use of SCM in the future. He speaks of extending use of the current Infor software to manage chocolate inventories, to enable better adherence to raw materials inventories, and to deliver more robustness in connectivity to the MRP process.
“With these basics in place there’s lots of little bits and pieces that we can now add on to make it a more complete environment,” Goodin concludes.
FURTHER READING
About This Vendor
More Case Studies

Rip Curl stays ahead of the wave
Doing business better in real time…

Charting a journey to operational excellence
Giving Veolia the ability to deliver requirements at short notice and improve their overall processes…

Nulon lubricates supply chain efficiency
Automotive manufacturer zooms into the industrial cloud…

Picking accuracy eliminates supply chain rework
Seed, fertiliser and garden products company Tui Products has taken back control of complex stockholding by implementing Infor’s Warehouse Mobility solution…

Bowron skins ERP solution for the future
Canterbury sheepskin manufacturer’s ERP implementation has set it on a firm footing for future generations…