Published on the 09/07/2014 | Written by Abel Software
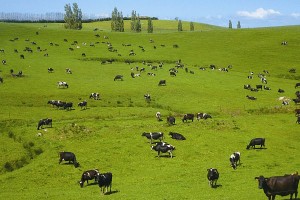
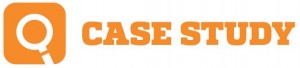
AT A GLANCE
INDUSTRY
- Manufacturing
BUSINESS OBJECTIVE
- ERP functionality across financials, inventory management, and production, planning and scheduling – to improve cost control, overall efficiency and use of resources.
- End-to-end supply chain visibility focused on improving quality control, traceability, responding quickly to quality and safety concerns, and ensuring consumer confidence.
SOLUTION
- Automated financial, inventory and manufacturing processes through Abel to reduce costs, better utilize resources, and improve quality control and traceability.
- An integrated business management system that tracks every batch of product to provide easy, real-time access to critical supply chain data for GMP managers and staff.
THE BENEFITS
- Flexible, integrated solution configured to meet the company’s unique needs.
- Easy rollout of new ERP functionality as required without significant upgrades and associated costs.
- Real-time quality control traceability ensures timely, accurate and targeted response to quality and safety issues.
- Improved overall confidence in quality control and safety systems.
FOR MORE INFORMATION
ABEL SOFTWARE
W: www.abelsoftware.com
Australia
E: davidm@abelsoftware.com
T: +61 2 9888 3355
New Zealand
E: davidm@abelsoftware.com
T: +64 9 442 4603
Leading infant formula manufacturer GMP Dairy chose Abel ERP software for its strong manufacturing features and supply chain traceability…
It’s no surprise that infant formula makers must meet stringent food quality regulations to safeguard the health of babies. Dairy product manufacturers in New Zealand and around the world face even tougher standards if they want to export to China – the world’s largest and fastest-growing infant formula market.
China introduced new quality measures for imported infant formulas to improve safety and consumer confidence after a number of quality problems. Exporters to China must now further demonstrate clear quality control over their entire manufacturing process – from the raw dairy products delivered to their factory to the finished goods shipped to China’s shelves.
That’s good news for GMP Dairy. An established leader in New Zealand’s $200 million export market for infant formula to China, GMP Dairy is particularly well positioned to meet both the new regulations and the surging demand worldwide for quality infant formula products.
One reason, says GMP Dairy Director Karl Ye, is the company’s new multi-million dollar factory – New Zealand’s first pharmaceutical grade dairy product manufacturing facility. With glistening stainless steel mixing equipment and epoxy resin floors, the 5,000-square-metre Auckland facility looks more like a scientific laboratory than a traditional factory. Built to strict hygiene standards with extensive automation, the clean room production facility features the most advanced dairy processing, air filtration and testing systems in New Zealand.
New Zealand’s Prime Minister John Key officially opened the factory in 2012. Since then, production has been steadily increasing and in the next few years is expected to reach 40,000 tons of infant formula a year.
GMP Dairy’s other significant advantage – something that brings together all the company’s expertise, quality standards and innovation – is its “Black Box” traceability process. Karl says that traceability is essential in the pharmaceutical industry and that GMP Dairy took years to develop its complex system. Using closed-circuit cameras, sensors, batch readers and X-ray machinery, the patented quality control system records data from key stages of the production process.
“Infant formula is an extremely sensitive product for especially vulnerable consumers, so it needs very high manufacturing standards,” Karl says. “By collecting critical quality control information about every can of formula, our traceability process gives customers more confidence and allows us to quickly target any quality issues.”
As well as infant formula, GMP Dairy also produces nutritional adult milk powder and organic milk powder products for New Zealand and overseas markets.
GMP Dairy is owned by GMP Pharmaceuticals and both companies use Abel. With its pharmaceutical pedigree, GMP had specific requirements for a new ERP system. GMP Dairy chose Abel’s integrated ERP system because it helped the company to easily and efficiently track and access all its quality control data. GMP’s 60 users now have real-time visibility of the entire supply chain.
“We chose Abel because they took the time to understand our unique business and configure the system to meet our needs,” Karl says. GMP Dairy decided to turn on Abel’s functionality gradually so they could manage the implementation in stages, starting with Financial and Inventory Management, Production and Quality Control and then Planning, Scheduling and BI Reporting.
“Traceability was critical for us…Abel has given us a better, more flexible system and has contributed to our overall success.”
One of the most critical tools driving traceability is batch tracking. Abel allows GMP Dairy to respond to a customer’s query about a product by accessing detailed production data on any can of infant formula. The data includes everything from the batch or cypher numbers of the materials, to production details, shipping details and even an X-ray image of the can’s contents.
Before Abel, traceability was managed using spreadsheets. Karl says the Abel way is fast, efficient and accurate – giving GMP Dairy greater confidence about quality control.
GMP Dairy will soon give customers direct access to product information from anywhere in the world. Using a mobile phone to scan a unique QR (Quick Response) code on individual products, customers will be able to see the composition of the product and other testing data. The QR code also helps customers verify a product’s authenticity and can also advise customers of a product recall or warning.
GMP stands for Good Manufacturing Practice – the “gold standard” for food, drug and pharmaceutical manufacturers. GMP Dairy’s innovative traceability process and pharmaceutical-grade production standards certainly impressed the Chinese government. After Chinese auditors inspected 13 New Zealand infant formula manufacturers in early 2014, GMP Dairy emerged as the cream of the crop. GMP Dairy was not only the first company to be registered by China for the export of infant formula products, but also the only company that did not need to take any corrective action to meet the new requirements.
Most of GMP’s infant formula already goes to China, and Karl says the company plans to increase exports to China and to other markets, including Korea, Singapore, Taiwan and Australia.
GMP saw how much Abel offered so they decided to adopt more of Abel’s functionality than they originally intended including Abel’s Material Requirements Planning (MRP). Next on the list is Document Management, and further adoption of Abel’s capabilities in Capacity Planning, Scheduling, KPI Management and Utilization of Resources.
“Abel has given us a better, more flexible system and has contributed to our overall success,” Karl says. “We now have real-time access to accurate and critical information, improved quality control and security, and a more efficient use of resources.”
Source: This article was originally sourced from Abel Software
FURTHER READING
About This Vendor
More Case Studies

New ERP provides help with the heavy lifting
Victor Hydraulics leverages Abel ERP for system replacement…

Cakes and donuts get a sweet ride with new ERP
Mitigating recall risk just one factor in new system for Original Foods Baking Co.…

Traceability adds unique factor for NZHF honey
Manuka honey exporter NZ Health Food Company has embraced ‘all-in-one’ ERP solution Abel…

Keeping customers atop the food chain
Bonson NZ packages up ERP success with Abel…

A honey of a solution for Taupo exporter
Cosana is enjoying sweet success with Abel ERP’s traceability, flexibility and ease of use…