Published on the 07/08/2019 | Written by Newsdesk
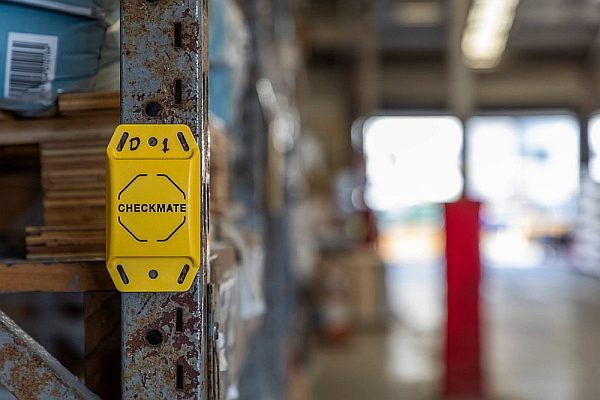
Checkmate is a safety compliance app on a mission – actual safety…
It may not seem like it on the shop floor, but health and safety at work is about a lot more than just clipboards and paperwork. Instead, it is a crucial function which should make sure that everyone gets home safely after each day. Sadly, this is not always the case. In worksites across New Zealand, up to 350 notifiable incidents take place every month. In the past year, 50 Kiwis showed up for work, but never made it home.
This raises an uncomfortable question: despite all the laws, rules and regulations, why are there still so many incidents – more than one a day – and why, every four days, does someone die at work?
Part of the problem could lie not in the rules themselves, but instead in how safety is done. It can be a cumbersome, paper-heavy process which inspires contempt, rather than compliance. That problem is a challenge a smart Kiwi start-up called Checkmate is setting out to address, with the introduction of a solution which automates, accelerates and digitises compliance, letting health and safety take precedence over paperwork.
Director Craig Shannon explains the idea behind the solution: “Nobody likes a busybody with a clipboard, but in terms of applicable health and safety regulations, and just plain good sense, regular checks and reports on equipment, work areas and other factors are absolutely necessary. To date, that’s been done with lots of paperwork and spreadsheets, which requires manual work including entering the data gathered into other business systems.”
[CONTINUES BELOW]
Video: Rusty Brooke, retail operations manager at Placemakers New Lynn
It’s a cumbersome process which was crying out for digitisation, as Andrew Stone from New Zealand’s Forklift Association makes clear. “It has been a substantial issue for businesses to prove that inspections have occurred. It seemed that all the standard operating processes need some type of inspection to occur on a regular basis, but to date there hasn’t been a system which actually engaged the team member, so they felt part of it and empowered.”
Building products supplier Fletchers is a Checkmate user and makes a further observation. “With over 350 pieces of mobile plant and over 15 kilometres of racking more than 3 metres high, the necessity for regular, effective and monitored checks is paramount. Until recently, these have all been completed on paper; this provided a range of challenges for us, including the quality of checks, when and if they were done and [questions around] escalation processes for defects,” says Anthony Mitchell, head of environment, health and safety at Fletchers Distribution.
Shannon notes that the problem with paper-based safety audits is that it’s difficult to quickly and easily check that all plant and machinery has been tested and is fit for purpose. “After all, what you have is a person wandering around with audit forms, or a sheaf of paper hanging on a peg next to a machine. If something isn’t up to scratch, it isn’t easy to see from that sheaf of paper – there’s no visual indication. Moreover, management might only find out days or weeks later. And by that time, more paperwork might be in the offing with a notifiable incident cropping up.”
Paperwork is notoriously error-prone, too, leading to additional shortcomings. For example, reporting of identified repair issues is often spasmodic at best. In some incidences, once a new week of audits starts, previous issues might fall off the agenda, with an assumption that they’d been resolved. In large companies with complex operations and multiple audits continually taking place, the problem is exacerbated in the absence of a reliable method of consolidating information, tracking audits and compliance reporting. “All that rolls up into significant and potentially severe risk; the risk of non-compliance and potential fines and reputational impact, and even worse, the risk that someone gets hurt,” says Shannon.
The digital answer
Checkmate’s solution combines a number of technologies which have long shown promise in multiple industries. They include an ‘Internet of Things’-like approach, in terms of which one of three different types of tags is fitted to equipment. These use near-field communication (NFC) to exchange data with a mobile device; that data is instantly collected and collated into a management dashboard which highlights issues according to a ‘safety light’ system: green is good and red means stop and don’t use this machine.
Shannon explains why different tags are necessary. “Some equipment needs an easy visual representation that tells operators at a glance if it is serviceable, so these Checkmate tags have an LED on them; if it shows green, the equipment is good to go. If red, it needs attention.”
Other tag types are programmable depending on the audit requirements for that machinery type. In conjunction with the Checkmate mobile app, workers scan the NFC tag, which brings up the specific audit checklist for that item, then perform the necessary safety checks, including adding notes or photos if needed. With the audit complete, a digital signature is appended, and the information submitted to a central database.
Built-in intelligence helps reinforce compliance requirements, notes Shannon. “For example, if audits aren’t done within stipulated timeframes, the system alerts the relevant parties, and the tags are programmed to guide checking of all parts of any particular asset, reinforcing approved processes.”
Central reporting is valuable in any business, but particularly so in large or complex concerns where there might be hundreds or even thousands of safety checks conducted on a weekly basis. Not only does it deliver a simple ‘heads up’ on any areas where compliance is in question, but it also provides the raw material for root-cause or common-issue analysis. This can contribute to the introduction of proactive measures that address shortcomings, further improving workplace safety and compliance.
From conception to production
The value of a digitised, automated solution for health and safety has perhaps been the best kind of validation in the rapid adoption of the Checkmate solution since its introduction. Conceived in early 2018, the necessary hardware and software was developed in just a few months.
Already, the company has racked up double-digits of industrial customers, including some of the biggest names in New Zealand business; notable among those is Placemakers, which has featured Checkmate in its ‘back to work’ video. The solution has been introduced across the business and is being adopted across the wider Fletcher Group.
Rusty Brooke, retail operations manager at Placemakers New Lynn says all Fletcher business units have an unyielding and stringent health and safety regime. “Checkmate certainly adds simplicity to that endeavour and is a very welcome addition to our armoury. The use of the system provides ease of operation, making it easy for the team to check all racking, mobile plant, saws and vehicles with absolute confidence – all the pertinent questions are populated onto the hand held scanning device.”
It doesn’t only make work safer; it also makes health and safety faster. Brooke explains: “We check over 250 items. These can be personalised to 30 mins, 1 hour, once a day, once a week or monthly all with no paper output and without a doubt has improved the compliance and quality of the audits across the business. It saves us time and money and the team loves it.”
Another customer which has rapidly seen the benefits of the Checkmate system is gym equipment distributor Blue Fitness. “We installed Checkmate at our Auckland distribution centre for a couple of reasons. Firstly, it streamlines the checking process of our machinery such as the forklifts, general building warrant of fitness systems and our pallet racking, storing this information securely online,” says Ben Davies, managing director at Blue Fitness. “Secondly, a number of our clients managing gyms are after a robust health and safety and equipment checking system and what better way to recommend a system than to implement it personally.”
Davies says the Checkmate system neatly ‘book-ends’ standard operating procedures which require inspections. “It means that the good intentions of a policy document or checklist can actually be recorded in real time at the actual site of the inspection. Team members like the fact that their check is recorded as real, and that follow-up required is managed once they note any issues. In short, Checkmate is a robust and useful tool to help businesses and their staff maximise their safety, while evidencing their efforts to do so.”
“Checkmate has recently expanded it’s operation into Australia and has attracted global attention, which has been rewarding to validate the investment and effort to date, and encouraging for further growth in the years ahead,” said Shannon.