Published on the 30/09/2022 | Written by Heather Wright
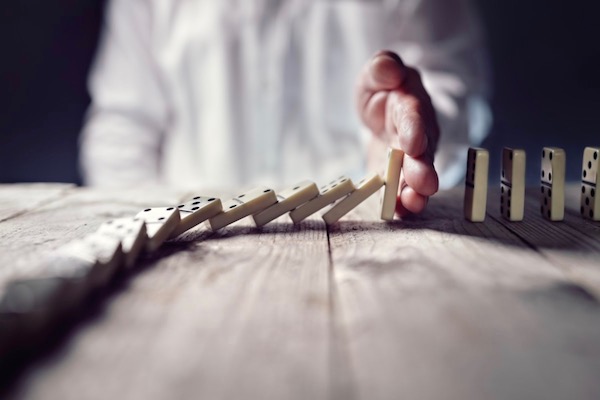
A path to supply chain resilience…
How much visibility do you have of your supply chain and how quickly can you respond to changes in your supply chain?
That’s the question Owen Keates, industry executive manufacturing practice for Hitachi Vantara, asks of local businesses.
The answers he fears, is not enough.
“There is evolution in maturity but it all starts with the ability to first understand and see your supply chain.”
“Globally there is an increase in companies looking at supply chain visibility as a very key step to helping them mitigate supply chain risk and putting a lot of effort into establishing the right teams and putting together the right technology to give them that visibility,” he says.
“But in Australia and New Zealand it is lacking somewhat, though rapidly picking up on the back of the ongoing exogenous threats we experience here.”
He believes the greater impact of Covid-driven supply chain disruptions in Europe and the United States has driven earlier adoption in those markets.
But with every business with an international connection impacted in one way or another by ongoing disruptions, he says demand in the local market for more visibility – and the ability to disrupt that disruption – is heating up.
“There is a high level of maturity locally when it comes to the internal supply chain management, so the ERP systems and running the sales and operations planning processes.
“But when it comes to the technologies around supply chain control towers and monitoring products from suppliers’ suppliers to customers’ customers, that’s a new area, and an area that is a lot more difficult to implement than many appreciate,” Keates says.
That’s largely due to the complexity of supply chains. Getting data from various stake holders along the supply chain, integrating with those systems and issues around ownership of the data, especially in agrifood, can make it an area fraught with challenges – but one Keates says is also ripe with opportunity.
The game changer, he says, has been the introduction of Industry 4.0 principles into broader sectors.
“As those principles have been adopted and sensors and sensoring systems have become more ubiquitous and a lot more cost effective to operate, the ability has arisen to be able to sense exactly where products and components are inbound and outbound. And if there is any product or component or produce that is temperature sensitive or has any other parameters that are critical in the distribution, you’re able to monitor those pretty cost effectively these days.”
It’s not just about visibility and bringing data back to a single pane of glass either, with advanced algorithms able to autonomously monitor and provide the appropriate decision support.
“That is the opportunity – leveraging the ability to sense those products and components inbound and outbound and monitor them in real time, autonomously while at the same time using the technology to scan the environment for external threats, whether extreme weather events, pending regulatory change, regional conflicts, whatever the threats are. You can have these AI systems monitoring for that so you can be alerted sooner rather than later.”
An Australian beverage company was able to rapidly reconfigure their supply chain to work around issues when the Brisbane river flooded and a key part of its supply chain was disrupted in the floods. It had used supply chain visibility and scenario planning to analyse and put in place a playbook for exactly that scenario.
“It’s one example of what companies are doing: Being able to essentially develop digital twins, look at their network, understand the current network configuration, and use the digital twin simulation to say what if that node got taken out, what would we do?,” Keates says.
“It’s one thing to have the information when it occurs, but unless you have a plan to enact it doesn’t help you much.”
But the process, he says, starts earlier – with what he calls the ‘descriptive stage’ where companies are just getting visibility through deploying sensors or integrating with external systems to ‘see’ their full supply chain.
“But you need to go beyond that because supply chains are very, very complex and the next step is to start being able to take that information and build a digital twin.”
And the step beyond that? That’s where the supply chain control tower concept comes into play
“Then you are monitoring your supply chain in real time, you have a digital twin that has been set up with a number of different scenarios and it is monitoring and connecting to the physical supply chain. And you start to have this symbiosis when there is a prediction that a disruption could occur, the digital twin component and the advanced algorithms on the digital twin start looking at different scenarios.
“There is evolution in maturity but it all starts with the ability to first understand and see your supply chain before moving up that maturity curve.”
He says for companies wanting to get on the curve to full visibility and decision support and actionable insights – and indeed supply chain resiliency – the first step is to identify the most critical supply chains with the biggest impact on the business.
“Very few companies have a single supply chain. There are many supply chains within the supply chain, so you need to have a look at where the biggest profit movers or the highest revenue components in the supply chain are – the ones that have the highest value at risk.
“Starting with that, work backwards from your facilities to your suppliers and their suppliers and understand at each point what the value at risk is. Do we have only a single supplier fo a critical component? Or do we have several alternative suppliers but they’re all in the same region and if there is an extreme weather event or disruption centred around that area it will be a problem,” he says.
“It is just understanding your second and third tier suppliers and then seeing what data is available to be shared with you and if data is not available see whether it is appropriate to jointly place sensors on critical components that can be recycled.”
It doesn’t have to be a big bang approach, he stresses, and building out over time with the involvement of key team members is a major win from a change management perspective, because team members understand where the data has come from, have been part of the prioritisation process and ultimately implementation can be a lot more efficient.
“These days many companies have a cloud solution where they have the core infrastructure in place and they can then start building the specific supply chain control tower algorithms on to the existing infrastructure.
“Others can use public clouds like AWS, Microsoft Azure or Google Cloud, who are all building up capability to handle this. And then there are companies like ours who are able to provide specialist solutions in all those areas, whether on one of those public clouds, whether building up on a customers exisiting infrastructure or a hybrid approach.”
For most companies working on supply chain resilience, including the ability to calculate Scope 3 greenhouse gas emissions using the same technology is also a ‘very serious consideration’, Keates says.
“So when they construct the data tables and architecture, they are building it in from the get go.”
Likewise, companies are increasingly including the ethical component in from the beginning.
“It’s holistically, looking at your supply chain from an ethical perspective, sustainability perspective and then from that business perspective making sure that you are designing your network to be as resilient as possible and to be able to proactively mitigate risk.
“Companies compete via their supply chains, so it is important to bear than in mind. At the end of the day, the most ethical and sustainable and profitable supply chain is the one that will win.”
But it’s not just about visibility. While that might be the starting point, Keates says