Published on the 16/08/2023 | Written by Heather Wright
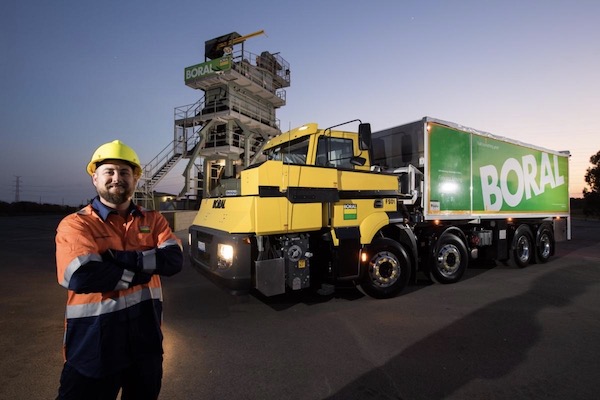
Customer, business benefits in new system…
Australian building and construction materials group Boral says customers are reaping early benefits as the company digitises its process chain, connecting trucks, products, plants and customer information to create a single source of consolidated data.
Boral Auto Allocations, which is being deployed across the company’s concrete business, is designed to improve order allocation process across Boral’s plants and fleet, improving on-time delivery, wait times and the productivity of the fleet.
“Further improvement is expected as we continue to roll out the program.”
The system uses algorithms to recommend the best transport schedule, taking into account customer service and transport efficiency, and adjusts schedules in real-time if, for example a ‘pour’ runs over time or there are traffic hazards on the road.
Boral says early data is showing improvements in customer service through increased on-time delivery to customers and more efficient transport.
“Further improvement is expected as we continue to roll out the program,” Boral says in its 2023 Annual Report.
The company says it recorded a nine percentage point improvement for delivery on time and a 27 point improvement in its grade of service in FY23.
The supply chain optimisation is being progressively deployed across the concrete business. It has recently been implemented in the metropolitan concrete plants in Queensland, Western Australia, Victoria and South Australia with metropolitan New South Wales scheduled to follow in FY24.
“The system’s pre-planning capability provides the contact centre, operations and sales teams with a shared view of the advanced schedule,” Boral says. “The visualisation tool allows collective decision making, helping achieve the best balance between customer experience and transport efficiency.”
The project is part of an ambitious decarbonisation campaign by the company, which also includes the use of renewable energy, alternative fuels and lower carbon concrete.
While the company says the enterprise standardisation program uses ‘world-class transport technology’, it hasn’t revealed exactly what technology is being used and did not respond to iStart’s requests for further information.
The company’s annual report also makes note of the use of a digital platform it has developed for ordering and order management.
Boral Connect enables customers to see current and future orders by status and job site address and is assessable from most devices.
The number of orders processed through Boral Connects nearly doubled in FY23, with the company saying it has established upgrade plans with implementation anticipated in FY24.
The company hasn’t been backward in its tech usage.
In 2020 it revealed it had cut US$1 million a year in cloud costs following a concerted savings push which saw it close down 50 percent of its cloud fleet most of the week and rightsizing resources to ensure it was only paying for what it needed.
Back in 2020, the company deployed a parking management system to increase efficiencies and flexibility, which enabled it to cut 35 parking spaces. It deployed Divvy Technology’s Enterprise system to manage the 220 parking spaces, using the real-time data to establish whether leased car parking spaces were being used to their full potential. The data provided insight into how many spaces were needed to meet staff needs and how utilisation could be improved based on staff working hours and needs.