Published on the 02/08/2018 | Written by Heather Wright
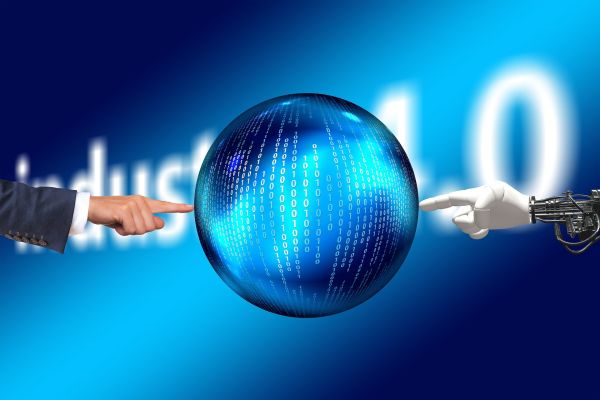
Is there a disconnect between IT ambitions and industry reality?…
Robot ‘employees’ with sensors and cognitive tools transporting packages around distribution centres; drone-based wireless systems scanning and locating items in warehouses; sensing systems, machine learning technologies, AI and automation in manufacturing – it’s the Industry 4.0 dream.
But is the dream nearing reality, or still just a distant mirage?
“As manufacturing goes through its next revolution, most developed countries are embracing Industry 4.0.”
Depending on who you listen to, Industry 4.0 – which has been around for a number of years now, but seems to be garnering new hype again this year – is either a fundamental shift for manufacturing, or a buzzword to describe the plod of progress.
At its essence, Industry 4.0 refers to the use of a broad set of digital technologies from process-aware software to robots, sensors, IoT, augmented reality, machine learning and ‘digital twins’ which will increasingly digitise and automate industry.
In January an Industry 4.0 report from suggested that industry was woefully ill-prepared for the ‘fourth industrial revolution’.
Chief among the concerns hampering Industry 4.0 is the changing skillset required by employees.
Now, a new report from Deloitte Insights highlights that technology-driven change can affect every function, including talent – particularly in the case of logistics and distribution, where established processes and ‘ways of doing things’ may be deeply entrenched.
The report stresses the people aspect as a key pillar, rather than a postscript, for Industry 4.0 programmes.
In the UK, manufacturers organisation EEF identified a lack of digital skills within companies as the biggest barrier to Industry 4.0, in which only 43 percent of businesses are investing, it says.
In Australia, an Industry 4.0 Taskforce was formed back in 2016 by the government, and signed a ‘cooperation agreement’ with Germany’s Platform Industrie 4.0, before the Australian Government passed the baton to the Australian Industry Group in 2017. The group “will lead the next phase of industry 4.0 activities, focusing on building education, awareness and collaboration between a broader cross section of industry’, the Government says.
Meanwhile in New Zealand the Employers and Manufacturer’s Association (EMA) has called on the government to create a new policy platform to promote Industry 4.0. Speaking earlier this year following the launch of Ministry of Business, Innovation and Employment’s Beyond Commodities: Manufacturing into the Future report, EMA CEO Kim Campbell said: “As manufacturing goes through its next revolution, most developed countries are embracing Industry 4.0 and its enablers such as 3D printing, artificial intelligence and the internet of things.
“New Zealand needs to be engaged in this process and a new policy platform is a vital next step in this process,” Campbell says.
The MBIE report said Industry 4.0 would see the creation of fully digitised smart factories, with intelligent software integrated with automated machinery to manage everything from inventory and customer orders, to manufacturing processes to scheduling maintenance and ordering spare parts.
While adoption of Industry 4.0 is likely to lead to fewer jobs, MBIE says those jobs will be more highly skilled – requiring upskilling of staff – and safer, with robots undertaking more hazardous tasks.
The report says ‘many’ firms profiled are already investing in capital and in the organisational know-how required for Industry 4.0, though specifics were somewhat scant.
Despite all the talk and initiatives, there is a reality check: It takes time for new technology to arrive on the factory floor. And there’s a good reason for that – you can’t have a factory running on bleeding edge technology. With their economic value, they need proven technologies and high levels of trust.
The reality for most manufacturers is that far from any revolution that the IT industry might tout, tech initiatives are cautiously and progressively implemented as they are tested, improved and productionised across similar facilities.
Of course as companies in the real world struggle to get on top of Industry 4.0, leading lights such as SAP are already pushing Industry 5.0, where products incorporating digital technologies ‘move from being a bundle of functionality and become platforms for value creation’.
But that’s a whole other story…